Introduction
This report describes an experimental program to evaluate corrosion of carbon steels in CO2 environment. Coupon exposure and electrochemical tests were conducted as a part of the program. The objective of the test program was to determine the corrosion rate of steel exposed to wet CO2 conditions. Test variables were brine chemistry, CO2 partial pressure, temperature, metal alloy and exposure duration.
The test program was performed in an effort to determine corrosion of metal alloys used in the transportation, injection and withdrawal of wet natural gas from a storage facility. Stored gas when retrieved would contain CO2 and reservoir brine over a range of temperatures and pressures.
Background
CO2 corrosion is a complex phenomenon that depends on numerous experimental variables. The key factor affecting iron dissolution in carbonic acid solutions (containing chloride) is the formation (or lack thereof) of an iron carbonate surface layer. Iron carbonate scales can be "protective" to provide low corrosion rates or "non-protective" meaning poor coverage, poor adhesion, porosity or solubility that provide higher iron dissolution rates.
The corrosion rate of iron in a CO2 environment is not constant, especially in laboratory studies in which the starting point is a bare metal surface on a test specimen. Steel, when initially exposed to a carbonic acid solution, corrodes rapidly at first and then the rate decreases as the carbonate scale forms. The final or "steady state" corrosion rate can remain high (if scaling does not occur), or it can asymptotically approach a limit that reflects ferrous ion (Fe2+) transport through the surface scale and other factors.
The dominant influence to the steady state corrosion rate of steel in CO2 environments is the aqueous phase chemistry and temperature. Low rates are promoted by conditions that favor film formation. Such conditions are not intuitive in the sense that several kinetic processes compete to produce either protective or non-protective scales. In brines, higher CO2 partial pressure, higher pH, higher temperature and low convection promote scale formation and low rates.
There is a temperature at which the CO2 corrosion rate is a maximum. The temperature at which the rate is a maximum depends on aqueous phase chemistry. When the brine phase is similar to seawater, the maximum is in the range of 60 to 150 F. Brine anions that favor scale formation and low rates are CO32-, SO42-, PO43-, NO3-, and SiO3-. Cations that favor scale formation are Ca2+, Mg2+ and Fe2+.
Experimental
The test program consisted of autoclave exposures of coupons to provide weight loss corrosion data and electrochemical corrosion rate measurements.
ApparatusA set of eight hastelloy lined autoclave vessels with a
pressure rating of 10,000 psig and a temperature rating of 550 F
were employed for the 30 day coupon corrosion tests. These
vessels were placed into an oven equipped with a rotisserie and
were rotated end over end to determine effects of fluid velocity
and to mix multiphase solutions. Illustrations of the autoclave
system are provided in
Figures 1
and
2.
Electrochemical testing was performed in a three liter hastelloy lined autoclave with a pressure rating of 5000 psig and temperature rating of 550 F. The autoclave was equipped with pressure ports into which were mounted the electrode holders. The vessel was also equipped with a pressure balanced silver/silver chloride reference electrode system that contacted the test solution by means of a Luggin probe.
MaterialsCoupons of X-42 carbon steel had dimensions of approximately 1.0 inches X 0.5 inches X 0.125 inches with two mounting holes located at one end of the coupon (See
Figure 3). A section of J-55 carbon steel tubular and machined additional coupons are procured for testing. Electrochemical tests employed cylindrical electrodes machined from X-42 stock as shown in
Figure 4. Two electrodes of X-42 and J-55 with dimensions of 0.250 inch diameter X 3.5 inches with one end drilled and tapped were machined for electrochemical linear polarization tests (See
Figure 4). Material chemistries are listed in
Table 1.
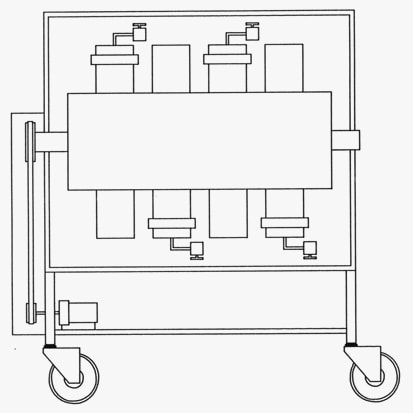
Figure 1 - Rotating Autoclave Apparatus
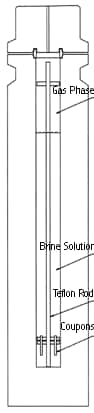
Figure - 2 Autoclave Configuration
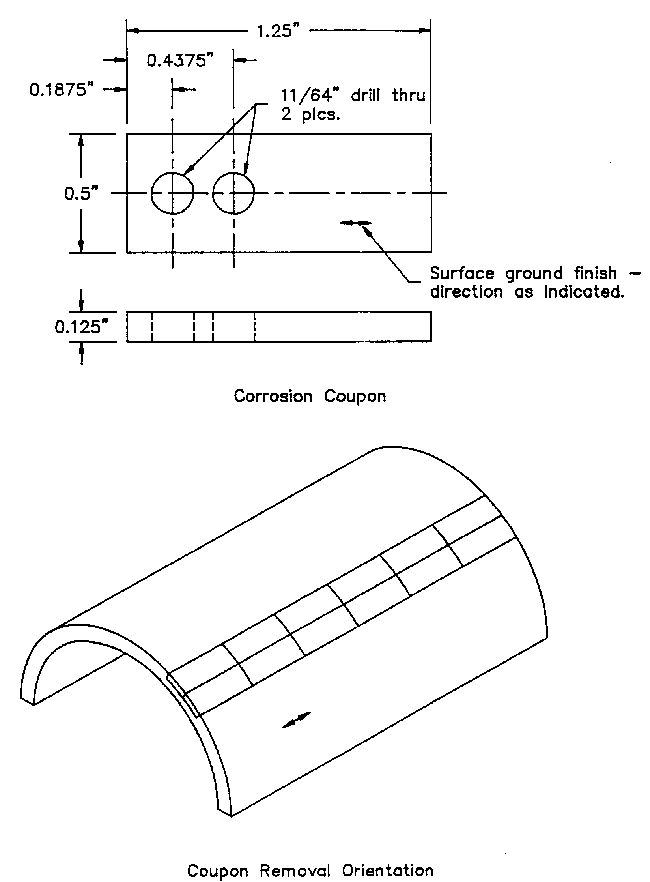
Figure 3 - Coupon Dimensions
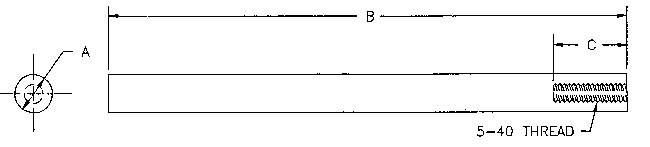
Figure 4 - Electrochemical Test Specimen
A - 0.25" ??
0.01" Dia.
B - 3.50" ?? ;
0.01"
C - 0.50" ??
0.05"
Note: The specimen is finished to surface roughness of 32 Micro-inch or finer
Grade | Carbon, max | Manganese | Phosphorous | Sulfur, max | Cb, min | Ti, min |
|
| min | max | min | max |
|
|
|
X-42 | 0.29 | -- | 1.25 | -- | 0.04 | 0.05 | -- | -- |
J-55 | -- | -- | -- | -- | 0.03 | 0.03 | -- | -- |